All you can PET
Plastic is bad for the environment, paper and glass are good. So far, so often wrongly generalized.
Thanks to deposit and returnable systems, a generally underestimated polymer is coming up trumps for drinks bottles: Polyethylene terephthalate – or PET for short.
We asked ourselves what the secret to the success of the most recycled plastic is. Where does it come from and where does it go and anyway...if PET is so great, couldn’t we just wrap EVERYTHING in it?
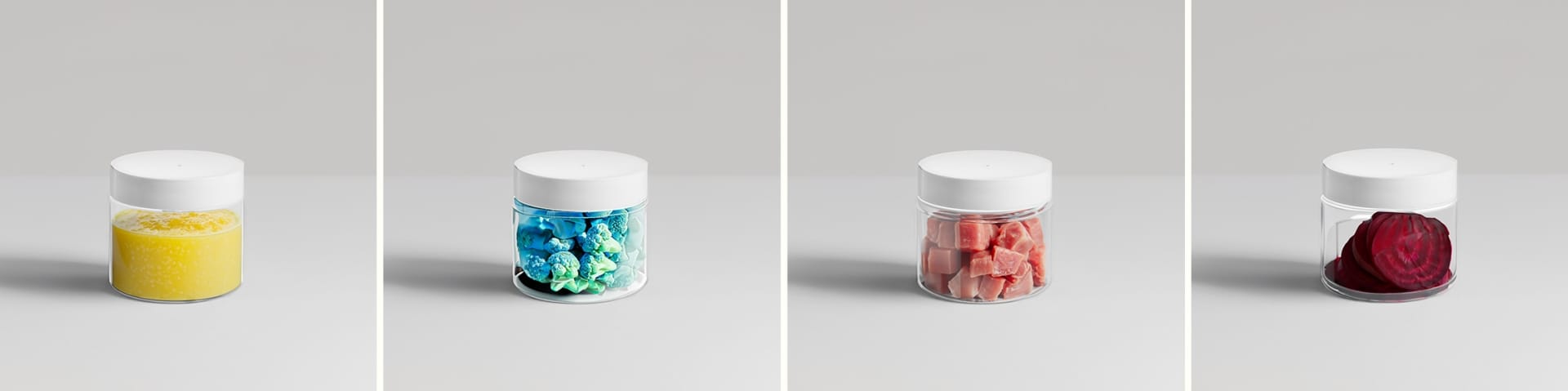
What actually is PET?
A small downer right at the beginning – yes, PET is a plastic made from fossil raw materials. Under normal conditions in nature, it decomposes so slowly that our great-grandchildren could still build bird feeders from the PET bottles that we throw into the environment today.
PET is a thermoplastic polyester that is formed during the polymerization of ethylene glycol and terephthalic acid. And even for non-chemists, it is a constant presence in everyday life, in the form of bottles, trays, films and textile fibers.
It is cheap to produce, easy to shape, transparent, durable and lightweight – that’s what it has in common with many other types of plastic. Nevertheless, it is the only type of plastic that can be used as a recyclate in the food sector according to EFSA regulations and produces “material-identical new products”.
Or, to put it more simply, it is the only plastic packaging for food that can be recycled into the same packaging in the current system. Some PET bottles are already very close to the dream of a circular economy, while other recyclates find their undignified end in thermal recycling after a second round as flower pots.
So what can PET do that other plastics cannot?
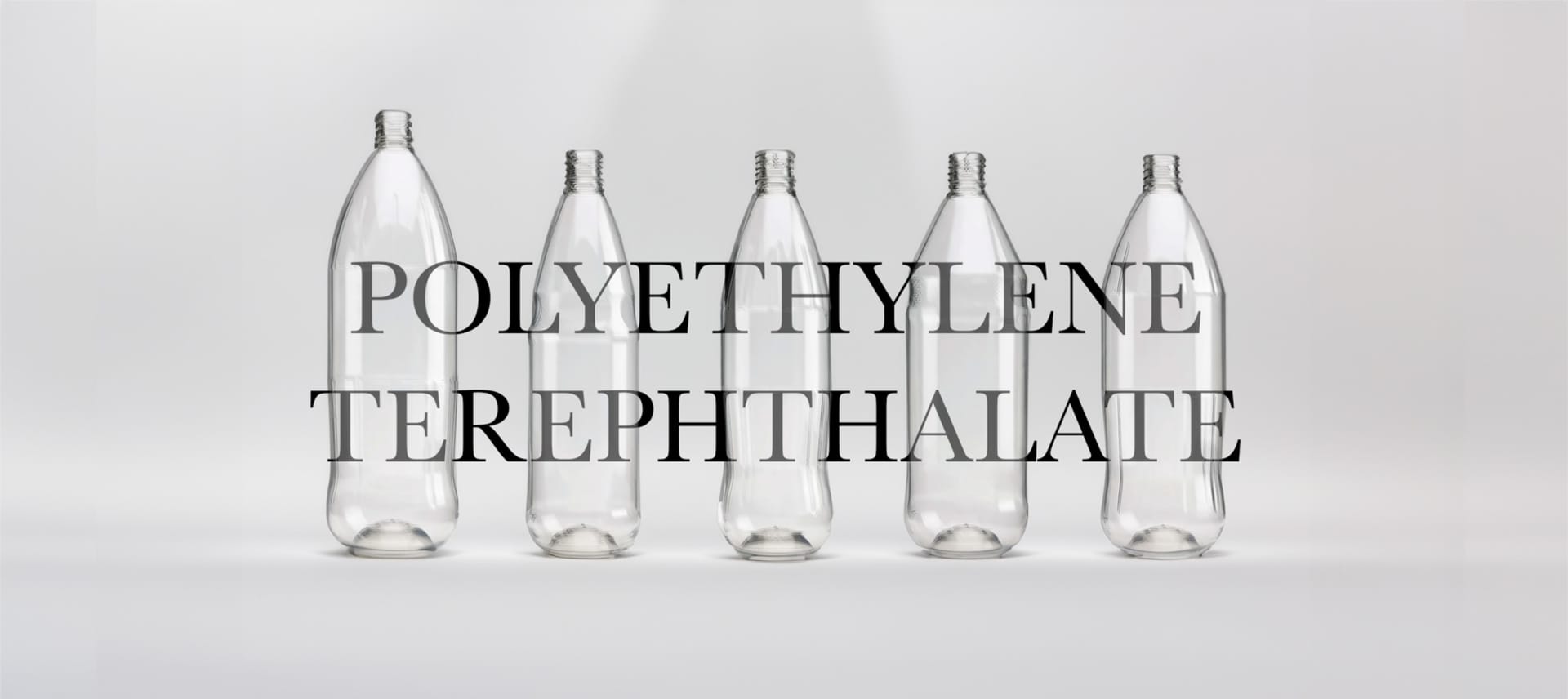
PET and the world of recycling
Basically: nothing. The green success of PET hollow containers is not due to the material itself, but to the circumstances of production and recycling. The design of many PET bottles is the dream of every design-for-recycling enthusiast: uncolored, standardized base bodies made of mono-material, easily detachable caps, easily detachable labels and little printed surface. The best basic prerequisites for mechanically recycling the material after use, i.e. washing, shredding and processing into new products. The whole process can be repeated up to 10 times on average, after which the quality is usually no longer sufficient.
The deposit system in Germany does the rest. Since its introduction in 2003, the return rate of PET bottles has increased to 90%. In 2022 alone, 1.8 billion bottles found their way back, with a deposit value of over 90 million euros. Reusable PET can be refilled up to 20 times and clearly beats glass in theCO2 race in logistics and production. PET is also ahead when it comes to future recycling technologies such as biotechnological recycling using enzymes. Numerous PETases from research are already in the starting blocks to get to the heart of our PET waste in the future.
So away with all the other polymers, PET for everyone and everything?
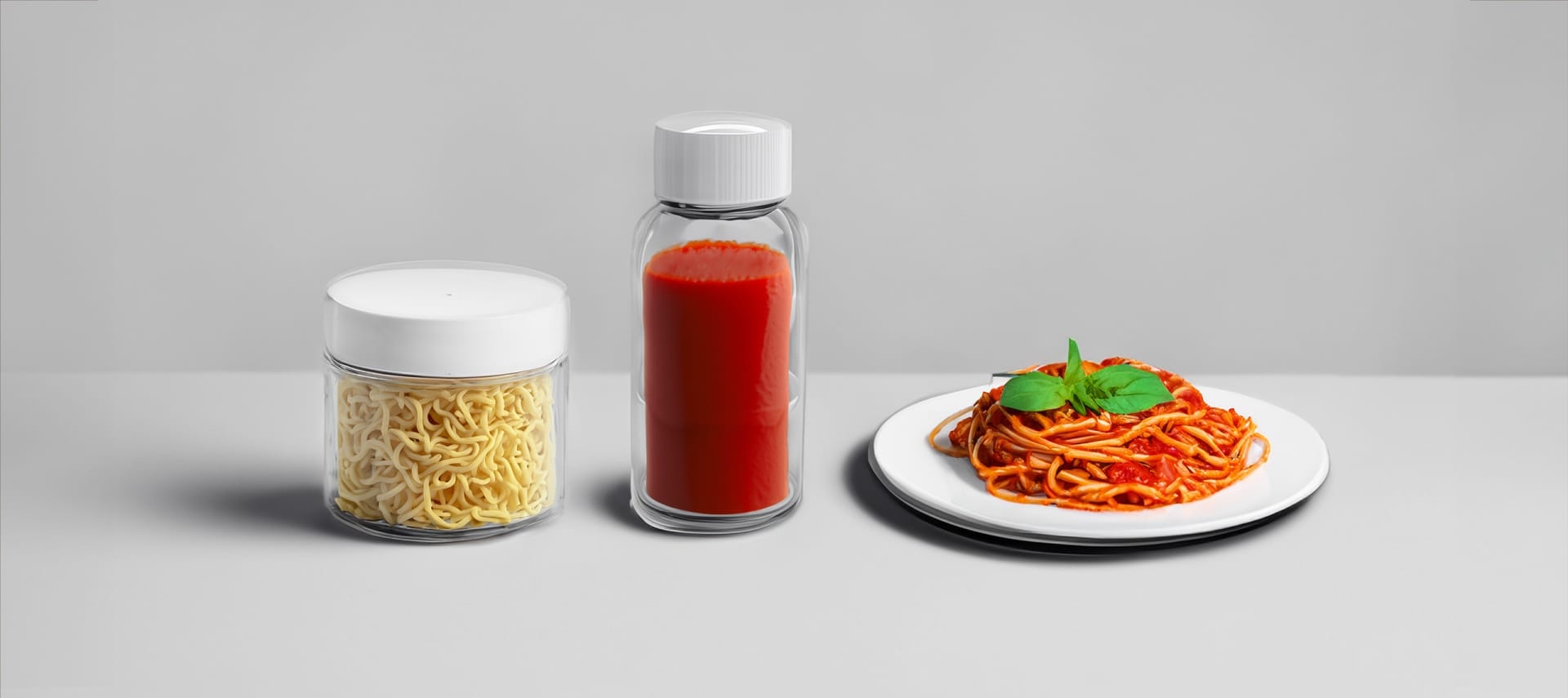
It’s complicated…
As always in the complex world of packaging, there are of course no such simple solutions. The success story of PET is currently still limited to returnable bottles. The average proportion of recycled material per bottle in Germany is approaching 50%. But even the bottles are often affected by downcycling – even if the soccer shirt of the German national team is probably a more dignified end than a flower pot. Other products made of PET, such as trays and cups, often have a different polymer structure or are composite constructions. Joint recycling would contaminate the beverage bottle stream. They are therefore incinerated in the same way as other post-consumer plastic packaging. In countries that have neither deposit nor mechanical recycling systems, anyway. The dream of an all-rounder for food is also disturbed by the fact that PET is susceptible to UV radiation. Unfortunately, this makes mono PET without additional barriers or additives unsuitable for highly susceptible foods.
To PET or not to PET?
PET is an integral part of our everyday lives and can be the best choice for food packaging from an environmental point of view. For many products that come in single-use composites (whether plastic or paper) today, there could be reusable solutions made of mono-PET tomorrow. If the EU’s forthcoming Packaging and Packaging Waste Regulation comes into force, there will be no getting around the expansion of multi-systems. According to this regulation, ALL packaging on the EU market must be recyclable by 2030 (this will be a tight squeeze for laminates). The minimum recyclate content for PET will be raised to 30% and single-use will be further banned from restaurants and delivery services. And these are just three of the many levers that (must) be pulled politically in order to move closer to the circular economy.
All you can PET needs More you can PFAND.
Conclusion: Only new closed systems with return incentives will deliver the quantity and quality of recyclates needed to achieve this goal. And only smartly designed products will meet the criteria set by such systems.
Manufacturers and designers must be prepared to change. Accepting visual flaws, avoiding colouring and large prints and standardizing shapes. Design for selling will have to give way to a certain extent to design for recycling . But every restriction also offers room for creativity – which we at MILK. in our Innovation Lab open up.
On the consumer side, however, we should learn to appreciate the pure sight of food again – but that can also be very aesthetic.
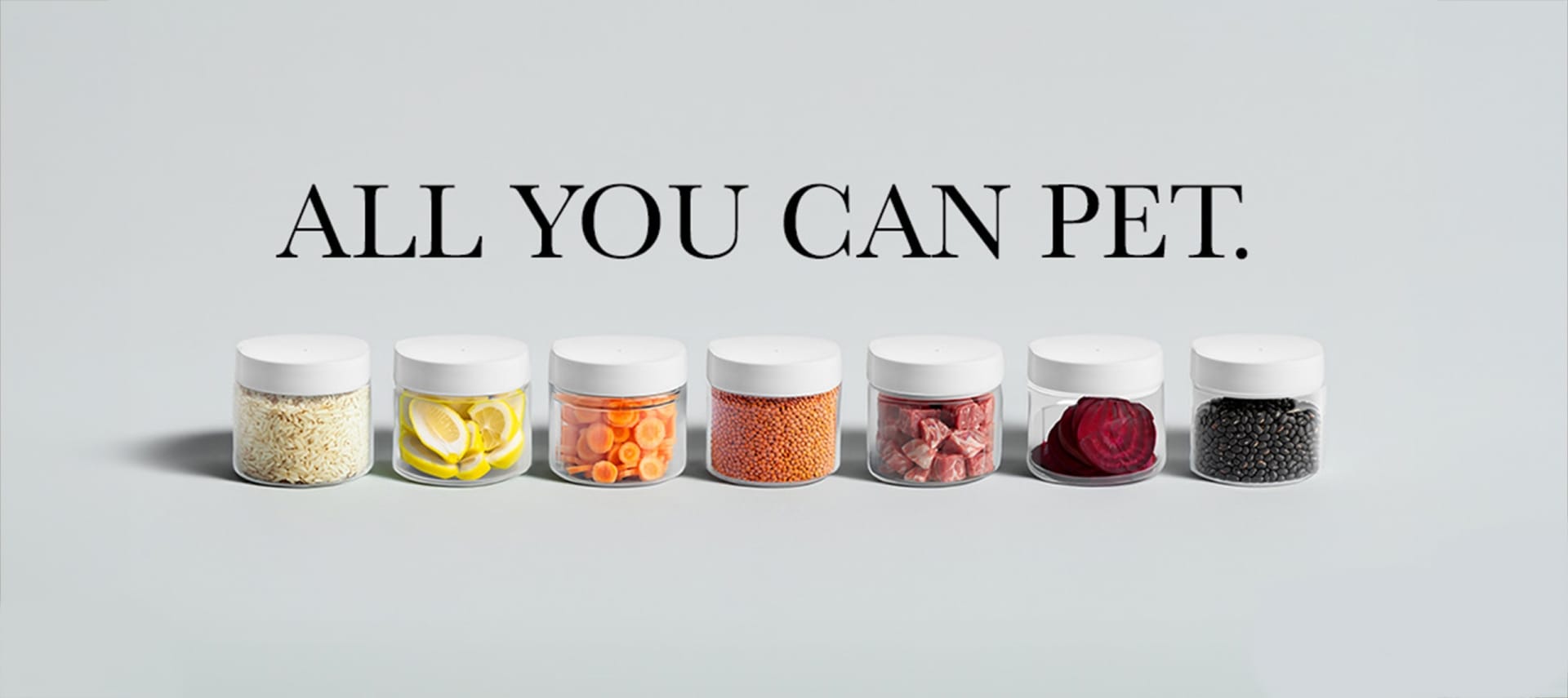