The triumph of fibers.
Two major influencing factors have led to plastic packaging being increasingly replaced by cellulose-based alternatives. On the one hand, paperization or fiberization is driven by consumer demand,
On the other hand, the paper industry is the big winner of the new PPWR regulation. While the plastics industry is being penalized and is working flat out to set up better recycling structures, many brands are switching completely to paper. Alfred Ritter, for example, has firmly anchored this strategically and is now busy with successive implementation. We were able to provide design support for this as part of the Ritter Sport mini relaunch and also like the idea of replacing some plastic packaging with barrier paper packaging.
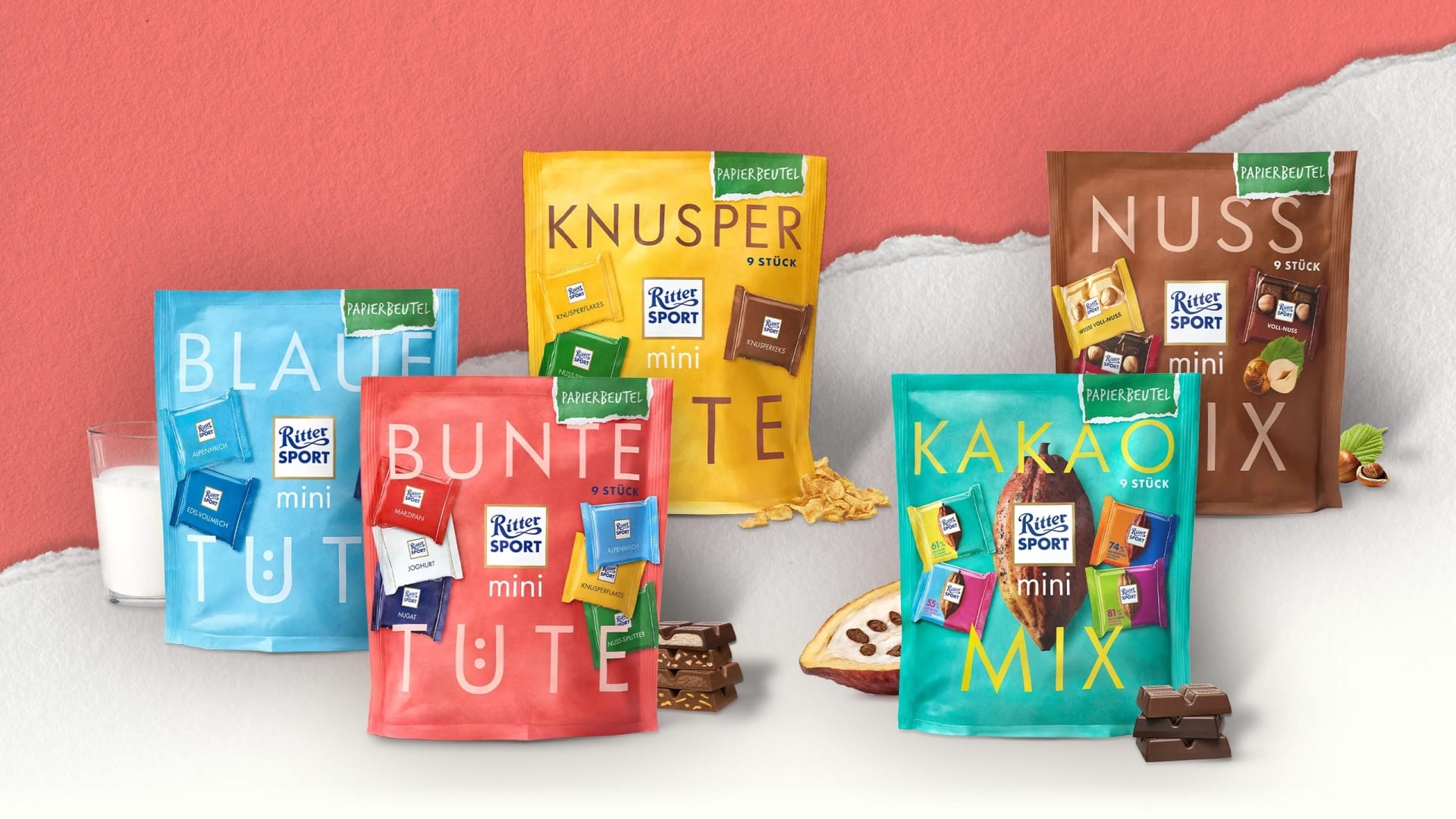
Image sources: Alfred Ritter, Nestlé
Wherever the barrier requirements allow, the high-performance securities come into play, which are now offered in a wide range of variants from small start-ups to large players. These replace plastic thanks to an ultra-thin barrier layer that can be reliably removed during the paper recycling process. It is not a composite material by definition because >95% of the packaging is paper fiber. The rest is coating, printing ink and, if necessary, varnish. As these are within the permissible proportion of impurities, they have a minor impact on the quality of paper recycling. However, as the amount of barrier paper in waste paper increases, the recycling industry faces a challenge. The final task for these promising packaging solutions is therefore to further reduce the proportion of impurities and adapt them to the recycling process.
Our conclusion: Papers such as the Koehler NexPlus Seal or Sappi Avantguard offer good barrier properties – but are of course not able to replace plastic 1:1 in every application. The newly announced plastic tax will also continue the upswing in barrier paper.
Best practice: Ritter Sport minis, Nestlé YES!